Alexandra G. McMahon, B.S., Research & Development Chemist, Koster Kuenen, Inc.
Belen M. Lemieux, M.S., Research & Development Laboratory Manager, Koster Keunen, Inc., lemieux@kosterkeunen.com
Abstract
Humans have been manufacturing soap since at least 2800 B.C., modifying and perfecting their recipes over the centuries. Today’s traditional soap bars are made via saponification of triglycerides: the alkaline hydrolysis of fatty ester bonds, leading to mainly C16-C18 fatty acid soaps and glycerol. In this paper, we explore the use of Natural Waxes from Koster Keunen, Inc. as starting raw materials in soap formulations, both alone and as additives to traditional triglycerides. Twelve Natural Waxes were blended with olive oil at 50/50 ratios, each blend was fully saponified, and the reaction products were evaluated for different properties and compared to a standard olive oil soap bar. It was determined through experimentation that each Saponified Natural Wax or Saponified Natural Wax Blend made a chemically complex finished soap, with different properties from the control and from each other. Some of the benefits encountered included improved bar hardness, a longer lifespan, more hydrophobicity, and innovative INCI declarations.
Introduction and Background
Few personal care products can have their history traced as far back as soap. While the historical accounts on soap and soapmaking are rife with legend, experts agree that the earliest evidence dates back to 2800 BC in Ancient Babylon, when a soap-like substance was discovered during an archaeological dig1.
Other records show ancient Egyptians, Greeks and Romans also made and used soap for thousands of years, perfecting the technique over time. By 1100 AD, soap making was an established practice in Mediterranean countries with easy access to olive oil, a key ingredient in Castille Soap, which was widely traded at the time2.
Soap was introduced to the Americas in the 17th century, when soap makers arrived in Jamestown, VA1. Over the next 200 years, as the United States industrialized, soapmaking evolved into one of the fastest growing businesses, with P&G’s Ivory being one of the first to gain national distribution3. However, food and fat shortages during World War I led German engineers to introduce synthetic replacements for soap, now known as detergents4. American consumers quickly embraced detergents due to their efficiency, availability, and low price; moving traditional soaps over time to niche market segments, particularly “Indie” brands, artisanal soap makers, and crafters5.
In recent years, and specifically at the onset of the COVID-19 Pandemic, the demand for hand soap has escalated. In fact, the global hand soap market is forecasted to grow by 6.7% from 2020 to 2030, with the household segment accounting for over 70% of the market share6. Although it is not clear what percentage of said growth refers to traditional soap bars (versus “syndet” bars or liquid detergents), current consumer trends, such as natural ingredient demand, small business support, and plastic reduction seem to support the persistence of traditional soaps7, 8.
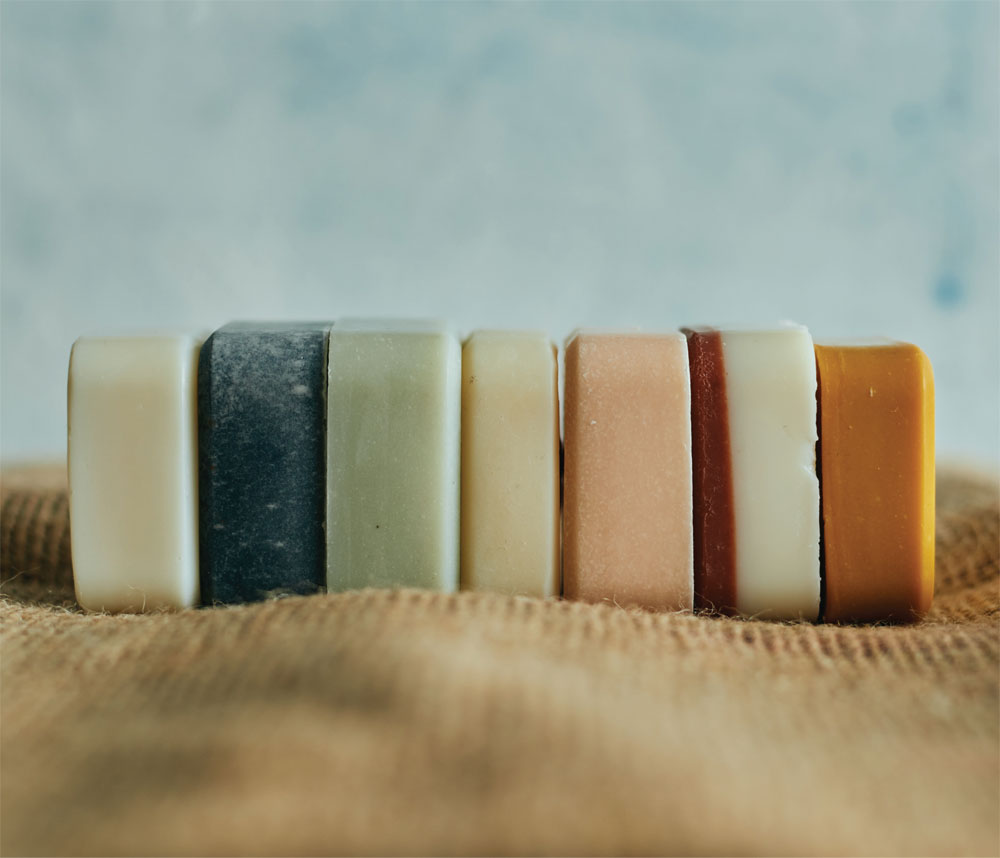
Soap Chemistry and The Role of Waxes
All soaps have in common one core recipe: Lipid + Alkali = Soap + By-product.
The chemical reaction that takes place is called saponification and can be defined as the alkaline hydrolysis of fatty ester bonds, resulting in fatty acid salts -the soaps- and a by-product (typically glycerol)9.
Most commercial soaps (and also DIY versions) are variations of “tried and true” recipes, based on well-known saponification reactions of well-known lipids, like tallow or palm oil10, with the only variations being in fragrance, color, and claim ingredients. This work is meant to encourage chemists and soap makers looking for innovation to vary the lipid source. This can be done by trying new ingredients, trying new combinations of known ingredients, or varying the ratios of these combinations. This will lead to new and innovative soap products, as well as by-products (often overlooked but important as well), which will affect the product performance, sensory aspects, and ingredient listing.
The Lipid Source
Lipids are a diverse group of organic compounds, characterized by their hydrophobicity and their biological importance. They present either as linear alkyl chains, saturated or with unsaturations, or as isoprene units in varying structures. These molecules may contain oxygenated substituents, such as carboxylic acids or hydroxyl groups11.
Traditional soapmaking would not be possible without a specific class of lipids, known as fatty acids. Fatty acids are linear alkyl chains, typically C12 – C22, saturated or with unsaturations, and a terminal carboxyl group12. In nature, fatty acids are typically found linked by ester bonds to glycerol, called triacylglycerols or triglycerides11 Due to this richness in fatty acids and widespread availability, triglycerides are the most prevalent starting raw materials in soapmaking. Some examples of lipid sources rich in triglycerides are tallow, palm oil, or olive oil13.
Waxes as Lipids
Waxes are a class of lipids with varying definitions and classification options. In a strict sense, waxes are comprised of long chain monoesters: long chain fatty acids esterified onto long chain alcohols with similar chain lengths, mainly saturated. A more practical description of waxes should include that they are blends of many components, including monoesters, hydrocarbons, sterol esters, and fatty alcohols14.
Many natural waxes are biosynthesized by living organisms to provide a protective barrier against environmental stresses. Due to their protective nature, waxes are widely used in personal care and OTC drugs to provide a barrier to human skin, and are staple ingredients in lip balms, hand salves, and body creams15. In this paper, we explore the use of natural waxes as starting materials for traditional soaps.
Waxes Make Complex Soaps
Traditional lipid sources used in soap making, like animal fats (very high triglyceride content, usually centered around C16 – C18 saturated fatty acids) or plant oils (very high triglyceride content, usually centered around C18 unsaturated fatty acids)13, will yield almost exclusively combinations of saturated and unsaturated C16 –C18 fatty acid soaps, and glycerol as a by-product. While these small differences in carbon number and degree of unsaturation can translate to subtle differences in a finished soap bar, the chemical richness and complexity of each natural wax will create soap bars with vastly different chemical compositions.
In addition to the C16-C18 soaps and glycerol described above, waxes can also yield very high molecular weight soaps (from C24 up to C38) and a broad molecular weight range of fatty alcohols as reaction by-products, while keeping their unsaponifiable materials intact. These higher molecular weight soaps are more hydrophobic than their traditional counterparts, resulting in harder finished bars with a longer lifespan. In addition, both the newly generated higher molecular weight fatty alcohols, as well as the existing unsaponifiables will also contribute to the overall hydrophobicity of the soap bar, improving the film –forming and skin protecting qualities of the bar15.
The reaction products obtained from the saponification of each major natural wax component are summarized in Table 1.
Major Natural Wax Component | Saponifiable? | By-Product | Natural Wax Example |
Monoesters | Yes | Fatty alcohols | Sunflower Wax, Rice Bran Wax |
Hydrocarbons | No | N/A | Candelilla Wax |
Fatty alcohols | No | N/A | Orange Wax |
Free fatty acids | Yes | Water (likely evaporates) | Beeswax |
Triglycerides | Yes | Glycerol | Bayberry Wax, Cocoa Butter |
Mono- and Diglycerides | Yes | Glycerol | |
Triterpenes / Derivatives | Possibly | Various | |
Other | Possibly | Various |
Table 1. Saponifiable Materials Found in Natural Waxes.
Objective
The objectives of this paper are as follows:
- Saponify multiple natural waxes and determine the properties of the reaction products.
- Determine the effects of adding different percentages of natural waxes to traditional soap recipes.
Experimental
MATERIALS: The following materials were used to conduct this experiment:
- Natural Waxes as described in Table 2, all provided by Koster Keunen, Inc.
- Olive oil (INCI: Olea Europaea (Olive) Fruit Oil) as the control and standard Columbus Vegetable Oils.
- Sodium hydroxide, purchased from Fischer Scientific, from which a 30% solution was prepared for use in all the saponification reactions.
Wax Name | INCI Name | Source | Broad Chemical Comp. | Average Sap Value (mg NaOH/g) | Melt Point (°C) | Appearance | State at Room Temp |
Bayberry Wax | Myrica Cerifera (Bayberry) Fruit Wax | Bayberry Fruit | Triglycerides, C16 | 155 | 40-55 | Light Brown to Olive Green | Solid |
Cocoa Butter | Theobroma Cacao (Cocoa) Seed Butter | Cocoa Beans | Triglycerides, C16, C18:0, C18:1 | 138 | 29-35 | White to Off White | Solid |
Soy Wax | Hydrogenated Soybean Oil | Crude Soybean Oil | Triglycerides, C18 | 135 | 62-72 | White to Off White | Solid |
Castor Wax | Hydrogenated Castor Oil | Crude Castor Oil | Triglycerides, C18:OH | 128 | 85-89 | Off White | Solid |
Kester Wax K-24 | Lauryl Laurate | Crude Coconut and Palm Oils | Low Molecular Weight Monoesters | 104 | 23-30 | Off White to Light Yellow | Liquid |
Kester Wax K-48 | Cetyl Palmitate | Crude Coconut and Palm Oils | Medium Molecular Weight Monoesters | 104 | 45-53 | White to Off White | Solid |
Orange Wax | Citrus Aurantanium Dulcis (Orange) Wax | Orange Peels | Fatty Acids, Phytosterols, Fatty Alcohols | 73 | 35-45 | Orange to Brown | Liquid |
Rice Bran Wax | Oryza Sativa (Rice) Bran Wax | Crude Rice Bran Oil | High Molecular Weight Monoesters | 70 | 77-82 | Yellow to Light Brown | Solid |
Beeswax | Beeswax | Bee Secretion | Esters, Hydrocarbons, Free Fatty Acids/Alcohols | 66 | 62-65 | White to Yellow | Solid |
Sunflower Wax | Helianthus Annuus (Sunflower) Seed Wax | Crude Sunflower Oil | High Molecular Weight Monoesters | 63 | 74-77 | Light Yellow | Solid |
Carnauba Wax | Copernicia Cerifera (Carnauba) Wax | Carnauba Palm Leaves | Esters, Free Fatty Acids, Hydrocarbons | 62 | 80-86 | Dull Yellow to Light Brown | Solid |
Candelilla Wax | Euphorbia Cerifera (Candelilla) Wax | Candelilla Shrub Leaves | Hydrocarbons, Esters, Free Fatty Acids, Resins | 43 | 68-73 | Yellow to Brown | Solid |
Table 2. Chemical and Physical Properties of Natural Waxes.
Methods and Procedures
- Saponification values for each Natural Wax in Table 2 were either obtained from the specification sheet provided by Koster Keunen, Inc. or calculated using the USP 401 Method16. The saponification values were then used to determine the amount of the 30% sodium hydroxide solution required for each saponification reaction.
- The saponification reactions were carried out as follows:
- Each Wax or Wax/olive oil blend was heated to approximately 80°C as Phase A and allowed to cool below 60°C.
- The appropriate amount of 30% Sodium hydroxide solution was also heated to 60°C as Phase B.
- Phase B was added to Phase A with sufficient mixing using a propeller mixer, while maintaining the temperature at 60 °C for approximately 25 minutes. The saponified blend was then immediately poured into a silicone mold and allowed to cure for 48 hours.
- After the 48-hour cure time, a pH testing at or below 10 confirmed the reaction was complete.
Experimentation
Each Natural Wax, as well as the olive oil control, was saponified individually (100%) and the reaction products were evaluated. In some cases, Natural Waxes did not make a commercially acceptable soap at 100% usage, as the bars were composed of a high level of unsaponifiables. To continue the experiment, each Natural Wax was blended with olive oil at 50% ratios, saponified, and the reaction products were evaluated and compared to 100% olive oil (control). We will refer to these blends as “saponified blends” for the remainder of this paper, and each one was evaluated within the following categories:
Quantitative Evaluation: Effect on Bar Rigidity.
Penetration values were measured on a Koehler K19500 penetrometer. The penetration of 100% saponified olive oil was recorded at 57 dmm (needle, 50g). The saponified blends measuring below 57 dmm proved to harden the bar, increasing bar rigidity, while the saponified blends measuring above 57 dmm proved to soften the bar, decreasing bar rigidity.
Tactile Evaluation: Effect on Bar Cleansing Properties and Lather
In a sensory panel performed internally (N=20); individuals were given specific hand washing instructions and asked to evaluate both the lather on the hands and the cleansing properties of each saponified blend against the olive oil control. Panelists rated each saponified blend as “increases,” “decreases,” or “no change.”
Sensory Evaluation: Effect on Bar Color and Odor
The same sensory panel was asked to describe the finished bar colors and odor. These subjective observations were determined by comparing each saponified blend to the olive oil control.
Practical Evaluations: Trace Level, Recommended Use Level, Recommended Applications
Trace Level was determined by a skilled soap maker based on how fast/slow each saponification reaction took place. The Recommended Use Level and Recommended Applications for commercial soapmaking were also determined for each Natural Wax.
Results
All results are presented in Table 3.
Quantitative Evaluation | Tactile Evaluation | Sensory Evaluation | Practical Evaluation | |||||
Wax Name | Effect on Bar Rigidity | Effect on Bar Cleansing Properties | Effect on Bar Lather | Effect on Bar Color | Effect on Bar Odor | Trace Level at 50°C | Recommended Usage Level | Recommended Applications |
Bayberry Wax | Hardens | Increases | No Change | Green | Yes | Very Fast | 100% | Artisanal |
Cocoa Butter | Softens | Decreases | No Change | Light Yellow | Yes | Slow | 100% | Layering, Pours |
Soy Wax | Hardens | Decreases | Decreases | White/Off White | No | Slow | 15% | Molds |
Castor Wax | hardens | Decreases | No Change | Off White | No | Slow | 15% | Molds |
Kester K-24 | Softens | Decreases | Decreases | Ivory | No | Slow | 50% | Drop Swirls |
Kester K-48 | Hardens | Decreases | Decreases | White | No | Average | 15% | Molds |
Orange Wax | Softens | No Change | Increases | Dark Orange | Yes | Average | 50% | Layering, Swirls |
Rice Bran Wax | Hardens | No Change | No Change | Light Brown | Slight | Fast | 15% | Layering, Designs |
Beeswax | Hardens | Increases | No Change | Ivory | Slight | Average | 50% | Textured Top |
Sunflower Wax | Hardens | Decreases | Decreases | Light Brown | No | Fast | 15% | Molds |
Carnauba Wax | Hardens | Increases | Increases | Orange | Yes | Very Fast | 50% | Artisanal |
Candelilla Wax | Hardens | No Change | Increases | Tan | Yes | Average | 50% | Embedding |
Table 3. Properties of Saponified Natural Wax/Olive Oil blends. 50% of Each Natural Wax was saponified with 50% Olive Oil and evaluated.
Discussion
The results in Table 3 indicate each Natural Wax tested brought forth very distinct characteristics and attributes in traditional soapmaking. It was also determined that certain waxes are not always a suitable addition to these traditional techniques. Specifically, Natural Waxes with high melt points, higher molecular weight components or hydrogenated triglycerides can pose some challenges in processing techniques and are therefore recommended as hardening additives at ≤ 15% use level. Despite these few specific challenges, we were able to conclude that the following Natural Waxes offer numerous advantages in soap making, whether at 100% usage or as an addition to traditional triglyceride formulations.
Bayberry Wax
Due to its high triglyceride content, Bayberry Wax is fully saponifiable and can be used alone to make textured, artisanal bars, or as an additive to impart a rustic texture, color, and odor.
Cocoa Butter
Presenting a high triglyceride content and a relatively low melt point, Cocoa Butter can also be used at 100% to make a naturally moisturizing soap. As an additive, Cocoa Butter can slow trace, allowing soap makers to achieve swirls and designs, or soften existing bars.
Lauryl Laurate
The saponification of Lauryl Laurate yields sodium laurate, which aids in a stable, fast acting lather. This, combined with the lauryl alcohol generated, allows for soft formulas and unique, jelly-like textures in higher percentages.
Orange Wax
Only partially saponifiable with a high phytosterol content, Orange Wax is recommended as a natural orange colorant (both in the bar and the lather it produces), fragrance additive, and bar softener.
Beeswax
Beeswax is useful in all soap formulations at different usage levels due to its free fatty acids and its ratio of saponifiable/unsaponifiable components. Beeswax adds tack and is primarily a hardening additive, while also maintaining the original soap characteristics like odor, color, or lather.
Candelilla Wax
Although Candelilla Wax is composed of 50% natural hydrocarbons, the free fatty acids present saponify readily, especially when combined with other triglycerides. Candelilla Wax also produces an excellent lather and an overall hard bar of soap. The natural color and odor are preserved.
Rice Bran Wax
Rice Bran Wax contains mostly high molecular weight monoesters and is an effective and inexpensive hardening agent in soap systems with no real effect on color, texture, or odor. Also high in palmitic acid, Rice Bran Wax also raises the possibility of replacing palm oil in low percentages.
Carnauba Wax
The hardening properties of saponified free fatty acids and high molecular weight monoesters present in Carnauba Wax helps to impart a firmer, long-lasting bar of soap with a dense, stable lather. Saponification also occurs much faster due to the higher percentage of unsaponifiables.
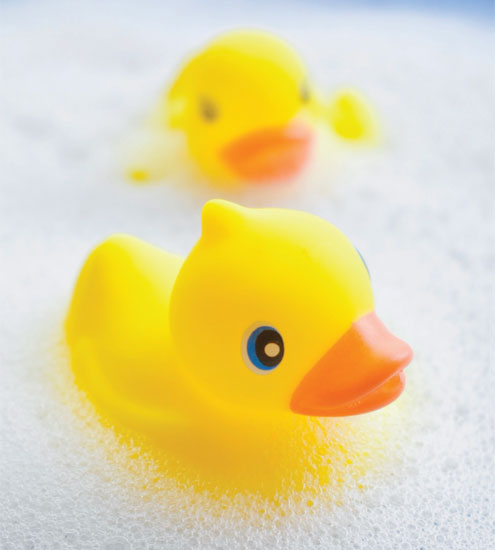
Conclusions
Although there is minimal information in current literature regarding the use and effects of Natural Waxes in soapmaking, possibly due to a very triglyceride-focused soap industry, the results of these experiments indicate the beginning of a relationship between the two. The uniqueness of each Natural Wax can be leveraged to create improvements in appearance, performance, and stability, setting the soap maker apart from the competition. In conclusion, incorporating Natural Waxes into traditional soap recipes allows for new formulas and more creativity, while keeping in alignment with a sustainable, natural future.
References
- American Cleaning Institute (n.d.). Soaps & Detergents History. Retrieved December 12, 2022, from https://www.cleaninginstitute.org/understanding-products/why-clean/soaps-detergents-history
- BearMoon Soap (2020, September 15). The Origins of Soap. Retrieved December 28, 2022, from https://www.bearmoonsoap.com/blogs/news/the-history-of-soap
- Koeppel, D. (2020, April 15). The History of Soap. Wirecutter. Retrieved December 21, 2022, from https://www.nytimes.com/wirecutter/blog/history-of-soap/
- Davidson, A. S. (n.d.). Early Synthetic Detergents. Britannica. Retrieved December 28, 2022, from https://www.britannica.com/science/soap/Early-synthetic-detergents
- Stephenson (2014, September 12). Soap vs. Syndet. Retrieved January 5, 2023, from https://www.stephensonpersonalcare.com/blog/2014-12-09-soap-vs-syndet
- MR (n.d.). Hand Soap Market. Retrieved January 11, 2023, from https://www.factmr.com/report/4718/hand-soap-market
- Moriarty, S. (2022, October 26). Mintel’s Global Annual Trends 2023. Retrieved January 13, 2023, from https://clients.mintel.com/content/trend/mintel-s-global-annual-trends-2023
- Prieto Vidal, N., Adeseun Adigun, O., Pham, T.H., Mumtaz, A., Manful, C., Callahan, G., Stewart, P., Keough, D., & Thomas, R.H. (2018). The Effects of Cold Saponification on the Unsaponified Fatty Acid Composition and Sensory Perception of Commercial Natural Herbal Soaps. Molecules, 23(9), 2356. https://doi.org/10.3390/molecules23092356
- Ashenhurst, J. (n.d.). Basic Hydrolysis of Esters – Saponification. Retrieved January 5, 2023, from https://www.masterorganicchemistry.com/2022/10/27/saponification-of-esters/
- Mintel (n.d.). Untitled. Retrieved December 13, 2022, from https://mintel.com
- Christie, W. W. (n.d.). Lipids: Definitions, Classification and Nomenclature. Retrieved December 29, 2022, from https://lipidmaps.org/resources/lipidweb/lipidweb_html/lipids/basics/Nomen/index.htm
- Rustan, A. C., & Drevon, C. A. (2005). Fatty Acids: Structures and Properties. In eLS (Ed.). John Wiley & Sons, Ltd. https://doi.org/10.1038/npg.els.0003894
- Coiffard, L., & Couteau, C. (2019). Soap and syndets: Differences and analogies, sources of great confusion. Eur Rev Med Pharmacol Sci, 24, 11432-11439. https://doi.org/10.26355/eurrev_202011_23637
- Christie, W. W. (n.d.). Waxes. The Lipid Web. Retrieved December 29, 2022, from https://lipidmaps.org/resources/lipidweb/lipidweb_html/lipids/simple/waxes/index.htm
- Eberting, C. L., Coman, G., & Blickenstaff, N. (2014). Repairing a Compromised Skin Barrier in Dermatitis: Leveraging the Skin’s Ability to Heal Itself. J Allergy Ther, 5(5). https://doi.org/10.4172/2155-6121.1000187
- General Chapter: USP. Fats and Fixed Oils – Chemical Tests and Assays <401>. In: USP-NF. (2022, May 1) DOI: https://doi.org/10.31003/USPNF_M99160_04_01