Products
Formulas
What are the benefits of a water-in-oleogel emulsion in personal care?
- Incorporation of both water and oil soluble actives.
- Increased emulsion stability.
- Flexibility: multiple levels of structure are possible.
- Innovative, interesting textures.
- Benefits of oil based formulas without the greasy feel.
- Possible cooling effects on skin.
- Sticks and other “on-the-go” formats.
What are the sensory benefits of a water-in-oleogel emulsion?
Because of this hybrid nature, w/og emulsions can offer both the positive sensory benefits of w/o emulsions as well as of anhydrous formulations. In a sensory panel, participants were presented with a trio of skin care formulations: a standard w/o emulsion, a structured w/o emulsion and an anhydrous balm, all based on the same formula backbone. Panelists were asked to rate and describe the sensory properties.
The sensory panel results show an overwhelming preference towards the structured w/o format, as well as a wider range of sensory/texture descriptors when compared to the corresponding w/o emulsion and anhydrous balm.
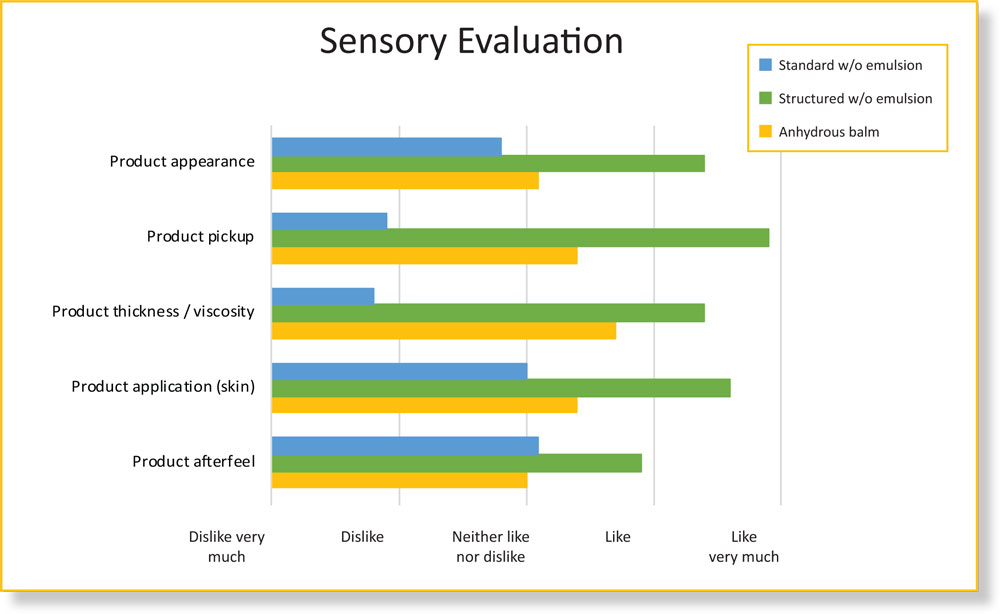
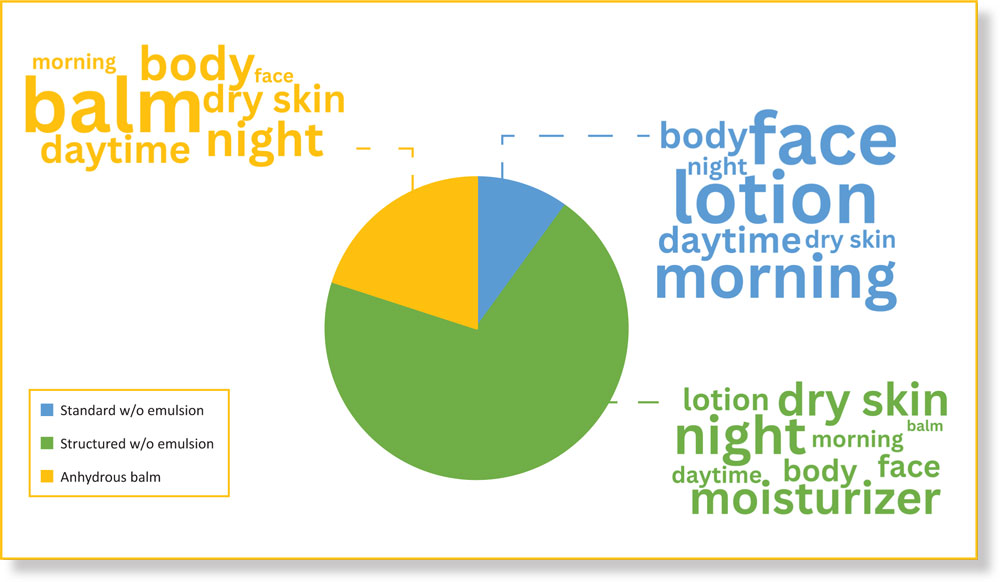
Overall format performance
initial observations and hypothesis
The addition of waxes in increasing levels to the oil phase of w/o emulsions (external phase) show very different results than those observed when adding waxes to the oil phase of o/w emulsions (internal phase). Those results are consistent with our observations when working with oleogels. Our theory is that if there is a direct correlation between the structural properties of w/og systems and their og counterparts, all tools and techniques chemists use when working with anhydrous systems can be applied to working with structures w/o systems.
objectives
- Create oleogel (og) charts showcasing the structuring properties of different waxes in different oil mediums.
- Create water-in-oleogel (w/og) charts: Replicate #1, but with 50% water phase dispersed internally using an appropriate w/o emulsifier.
- Compare charts from #1 and #2 and determine any relationships. If they exist, test our theory on complex formulas and provide formulators with the tools and guidance to create their own systems.
oleogels theory and gel charts
Oleogels (og) are viscoelastic materials comprising a nonpolar liquid phase (the oil) and a gelator or mix of gelators, very typically waxes. Waxes immobilize the lipid phase through the formation of three-dimensional networks, resulting in systems of varying consistencies and firmnesses, largely dependent on the amount of wax used.
This oleogel firmness or strength can be measured with a penetrometer and recorded on a gel chart, a tool that can organize gel strength data in a meaningful way and save a lot of trial-and-error time. Gel charts published here were built by plotting penetration distance on the y-axis vs. % wax on the x-axis for each individual gel following the simple formula:
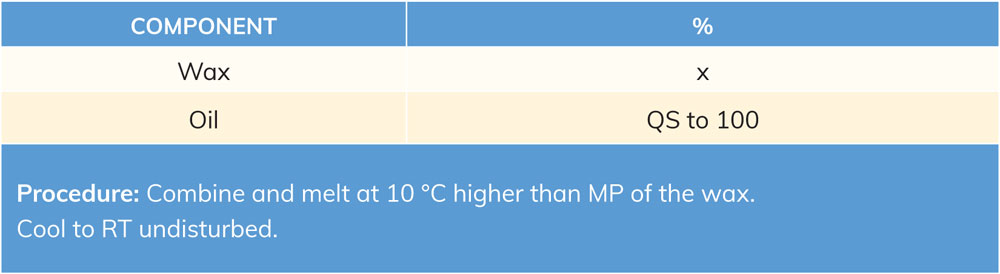
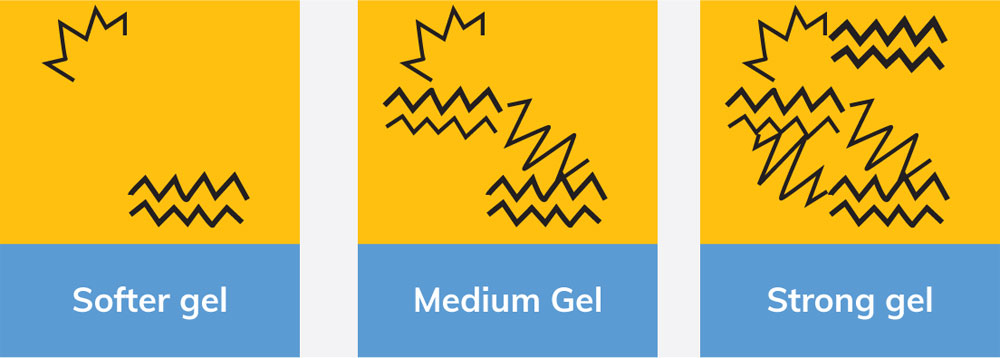
By overlaying different series on the sa me chart, we can see how the same wax behaves in different oils or how different waxes behave in the same oil.
wax selection
Waxes were selected to cover a wide range of structural and textural needs, as well as other formulation requirements. Specifically, we chose a strong, a medium and a soft gelling wax from both natural as well as synthetic origin: Sunflower Wax, Beeswax, Rice Bran Wax, Ozokerite Wax, Microcrystalline Wax, and Kester Wax K-82P.
oil selection
Caprylic/Capric Triglyceride (CCT) is listed as the most prevalent cosmetic oil in formulations containing wax*, so it was chosen for the majority of our studies.
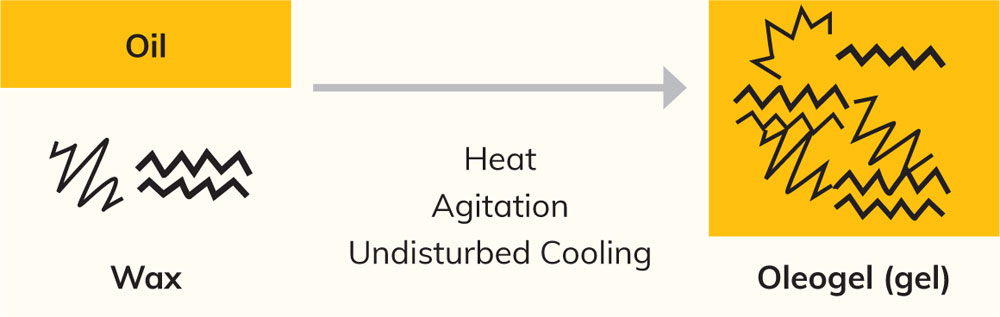
*According to Minte
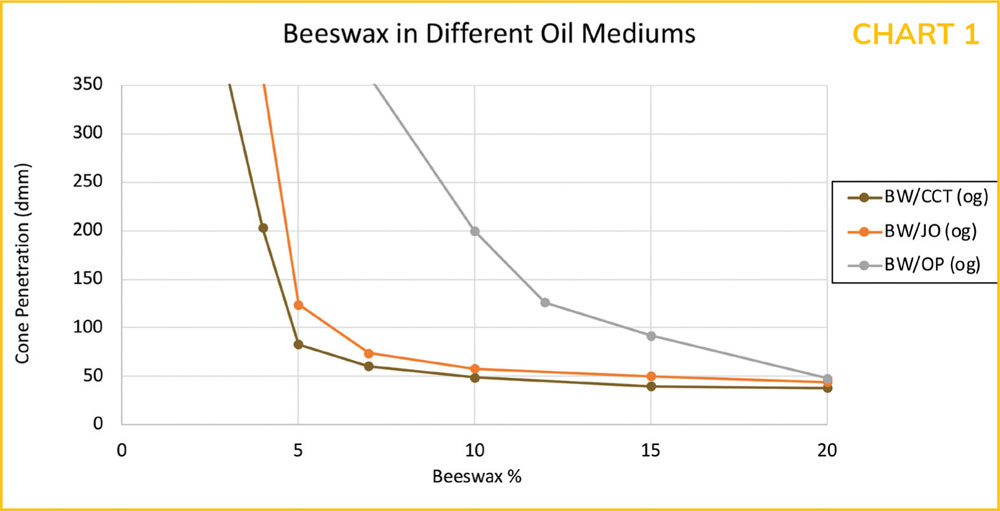
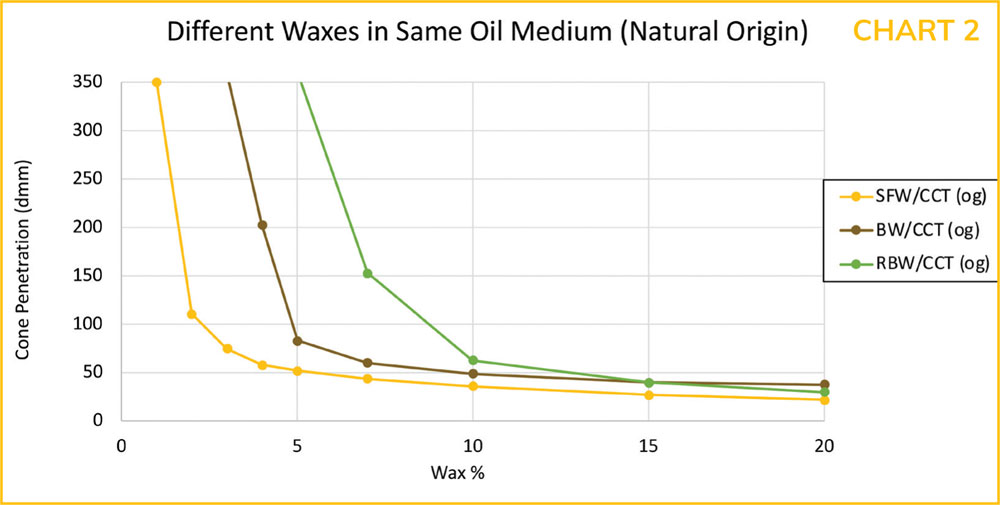
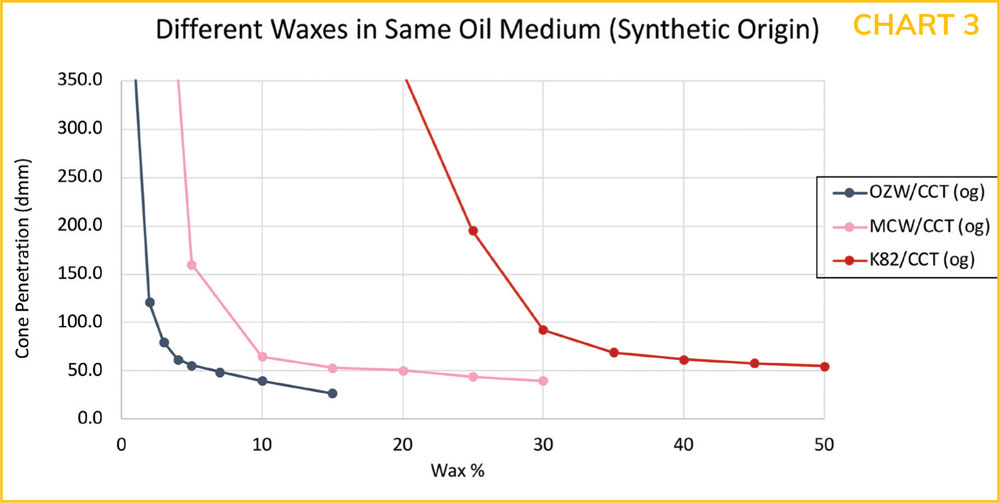
water-in-oleogel emulsions. theory and W/OG charts.
Water-in-oleogel emulsions (also called structured w/o emulsions) are different from conventional w/o emulsions, in that the internal (water) phase is dispersed in an oleogel network, which will have different degrees of immobility or gel strength, depending on the amount of wax incorporated. Water-in-oleogel (w/og) emulsions tend to be more stable than their w/o counterparts, because the internal water droplets are stabilized by more than one mechanism: presence of an appropriate w/o emulsifier, immobility that the gel network provides, and the Pickering effect that the waxes themselves provide.
Many w/og emulsions are firm enough that their strength can be measured with a penetrometer, allowing us to plot penetration distance on the y-axis vs. % wax on the x-axis, exactly like we did with their oleogel counterparts. The formulas are more complex, and follow the below model: on the y-axis vs. % wax on the x-axis for each individual gel following the simple formula:
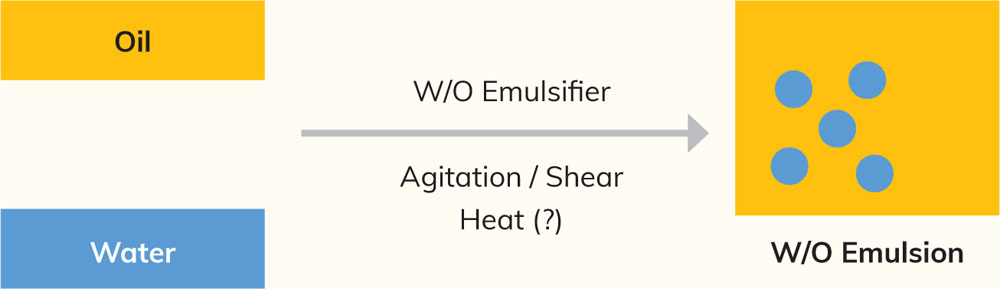
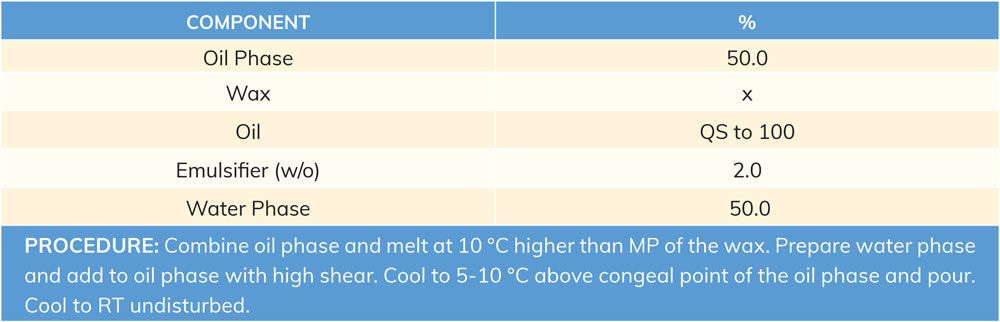
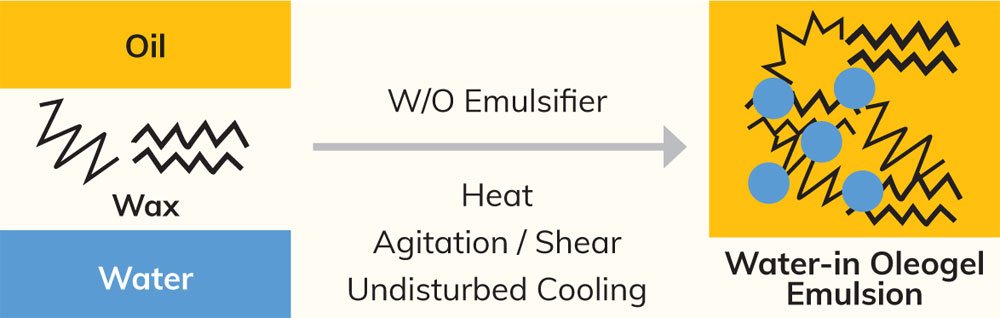
wax and oil selections
Wax and oil selections matched the selections from the oleogel charts. The emulsifier used throughout was polyglyceryl-3 polyricinoleate, and the water phase was made of 45.5% water, 3% glycerin, 0.5% phenoxyethanol, 0.5% NaCl, 0.5% MgSO4.
Penetrations were recorded and plotted on water-in-oleogel charts. Charts were overlayed in a way that allowed us to see the influence of each wax and of different oils in structured w/o emulsions.
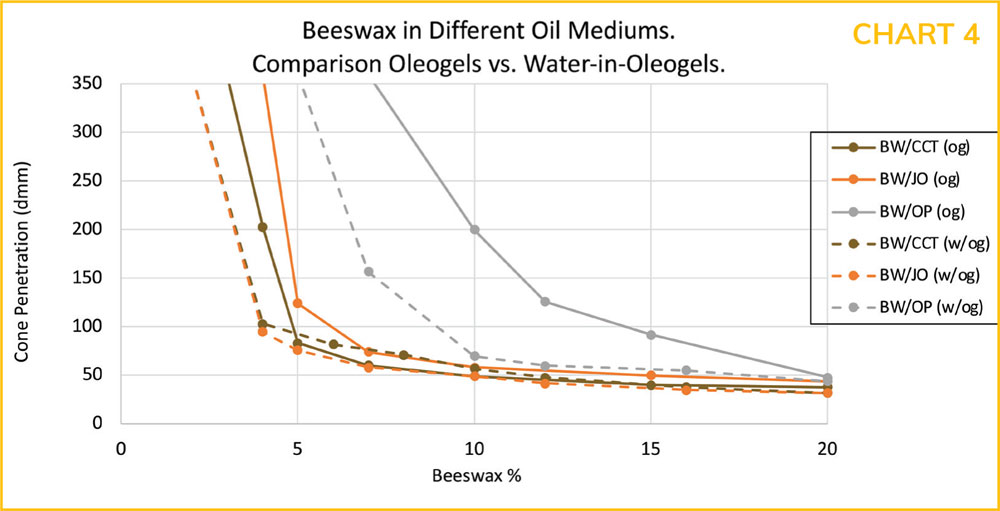
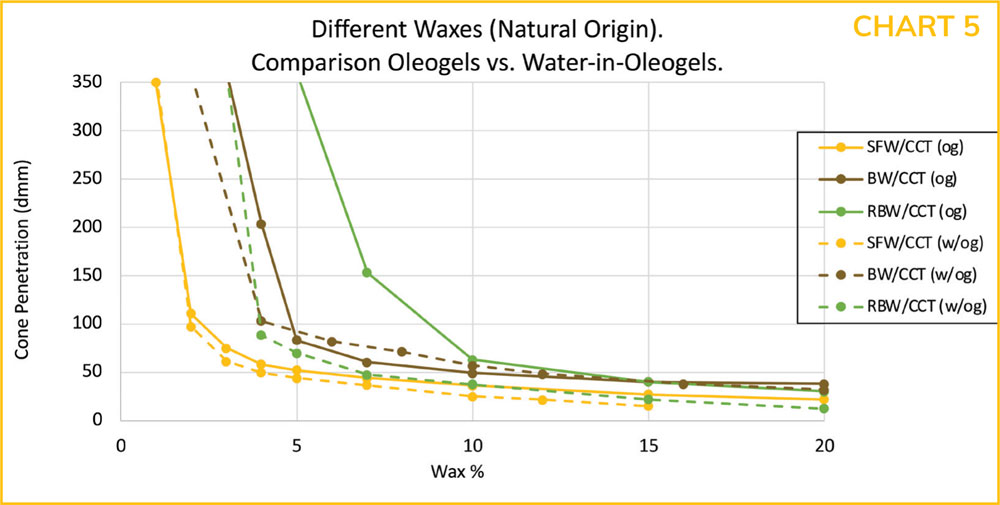
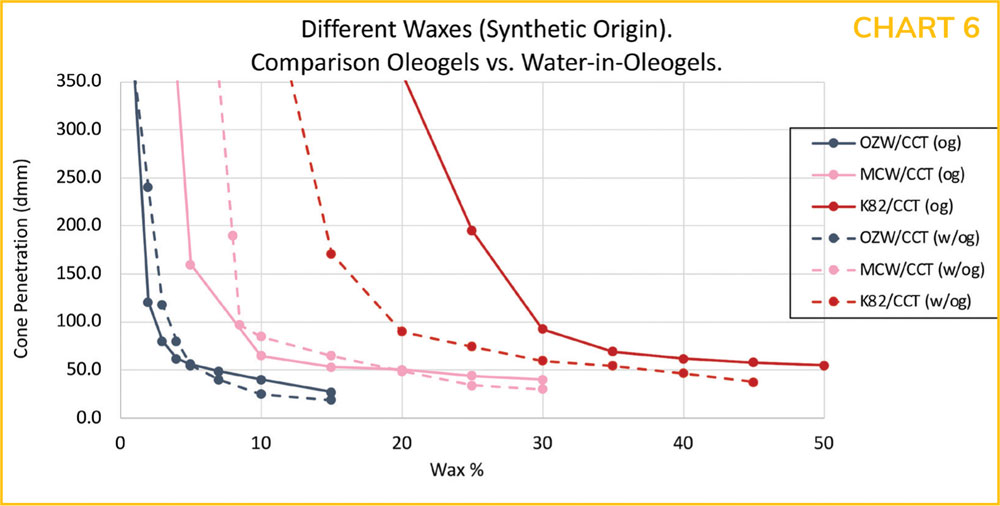
how to design structured W/O emulsions
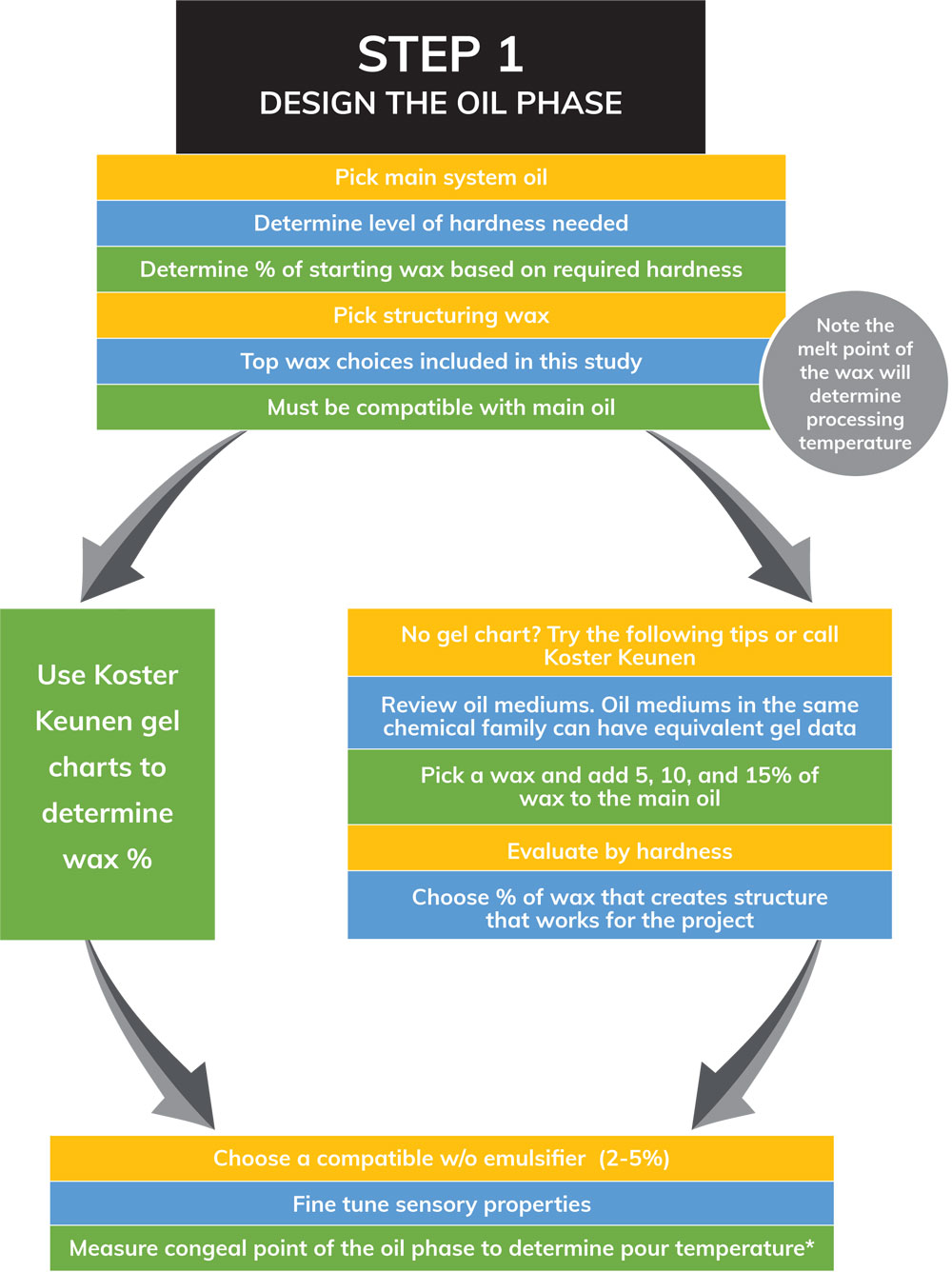
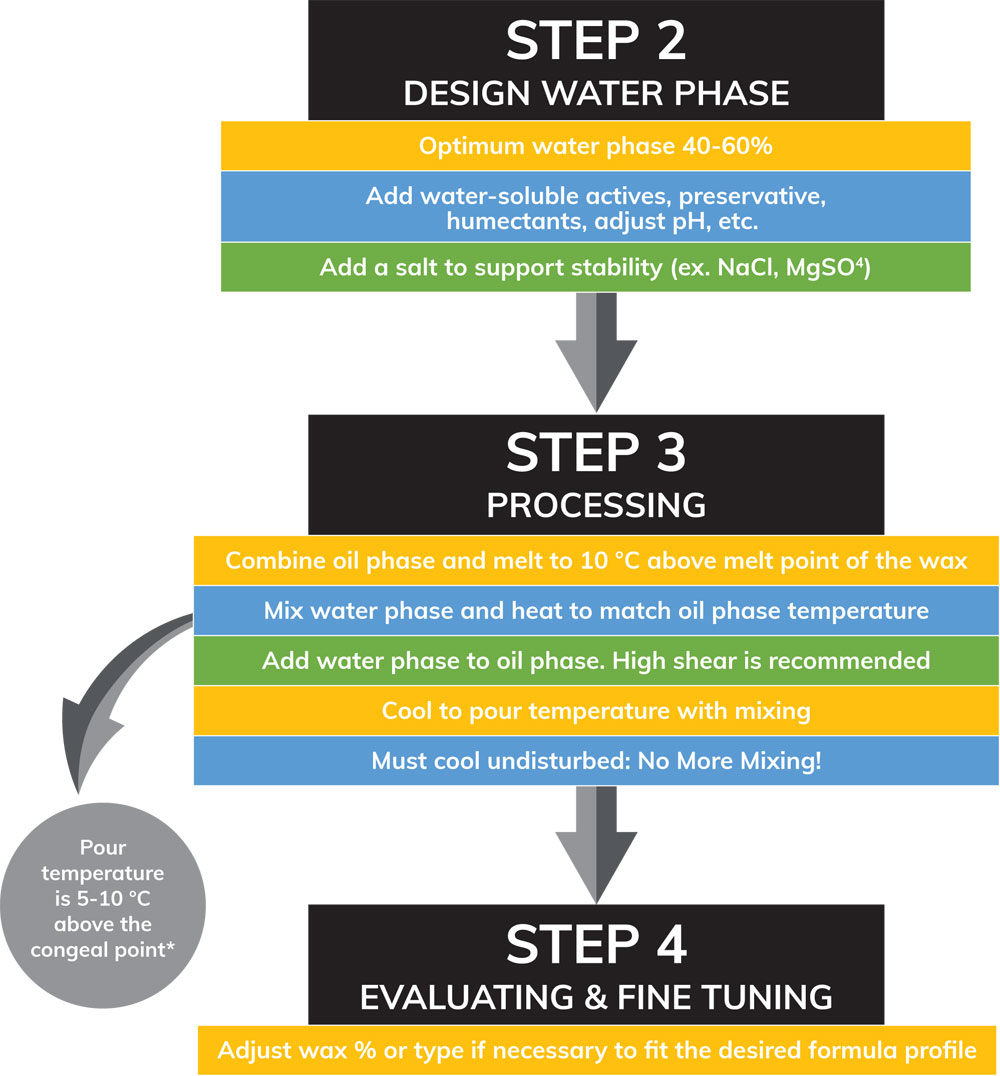
results. discussion
By overlaying gel charts (Charts 1-3) with the corresponding water-in-oleogel charts, we see the hardness of structured w/o emulsions is directly related to the hardness of their corresponding gels.
conclusions
- The properties of structured w/o emulsions are dictated somewhat by w/o emulsion theory, but much more so by oleogel theory.
- Chemists trying to build structured w/o emulsions can easily reference existing gel charts or use any other current knowledge of gel theory to predict the structure of their system.
- Exceptions can occur with weaker gel profiles
practical approach. complex formulas.
To test our conclusions in realistic formulas and further understand these systems and their processing needs, our lab created four innovative formulations made using the principles learned during our research and detailed in the outlined flowchart.
formula #1:
Soft, thick cream with a texture. Natural beeswax is encouraged.
Soft, scoopable balms will generally have a penetration of 70-150 dmm.
1. Design water phase
2. Design oil phase:
2.1. CCT was chosen as the main oil
2.2. Wax selection and % usage: Beeswax
2.3. According to Chart #4, 5% Beeswax with CCT as the main oil should yield the desired penetration
2.3.1. The melt point of Beeswax is 62 -66 °C, hence processing temperature will be 75 °C or more
2.4. The emulsifier was chosen due to compatibility
2.5. Measure congeal point of the oil phase. Results: 50 °C
2.6. Therefore, pour temperature will be 55-60 °C
3. Final formula hardness = 87.0 dmm
overnight repair cream
Formula # 6/23-421/358-6
Ingredient Trade Name | INCI Name | % |
---|---|---|
Phase A | ||
Beeswax | Beeswax | 5.0 |
Kester Wax K-24 | Lauryl Laurate | 9.4 |
Lipex SheaSolve | Shea Butter Ethyl Esters | 4.3 |
Canola Oil | Canola Oil | 3.4 |
Jeechem CTG | Caprylic/Capric Triglyceride | 12.9 |
Akoline PGPR | Polyglyceryl-3 Polyricinoleate | 5.0 |
Phase B | ||
Deionized Water | Aqua | 55.0 |
Optiphen | Phenoxyethanol, Caprylyl Glycol | 0.5 |
Glycerin | Glycerin | 3.8 |
Magnesium Sulfate | Magnesium Sulfate | 0.7 |
Procedure
- Combine Phase A ingredients and heat to 75 °C.
- Combine Phase B ingredients and heat to 75 °C.
- Once both Phases are at temperature, add Phase B to Phase A and mix using high shear.
- When emulsion is smooth, pour at 55 -60 °C into appropriate containers. Keep mixer on during filling.
formula #2:
Natural hard shell make-up remover and moisturizer in one.
Harder balms that require digging will fall in the 40-70 dmm penetration area.
1. Design water phase
2. Design oil phase:
2.1. Sweet almond oil was chosen as the main oil
2.2. Wax selection and % usage: Sunflower Wax
2.3. According to Chart #5, 5% Sunflower Wax in sweet almond oil should yield the desired penetration
2.3.1. Note: Although Chart #5 is specific to CCT, the data can be used to predict oleogel penetration in different oils, provided they are in the same chemical family
2.3.2. The melt point of Sunflower Wax is 74 -77 °C, hence processing temperature will be 85 °C or more
2.4. The emulsifier was chosen due to compatibility
2.5. Measure congeal point of the oil phase. Results: 62 °C
2.6. Therefore, pour temperature will be 67-72 °C
3. Final formula hardness = 55.0 dmm
Not Your Mothers Cold Cream
Formula # 3/23-258/358-3A
Ingredient Trade Name | INCI Name | % |
---|---|---|
Phase A | ||
Sunflower Wax | Helianthus Annuus (Sunflower) Seed Wax | 5.0 |
Kester Wax K-24 | Lauryl Laurate | 11.0 |
Cetiol CC | Dicaprylyl Carbonate | 11.0 |
Almond Oil | Prunus Amygdalus Dulcis (Sweet Almond) Oil | 16.0 |
Isolan GPS | Polyglyceryl-4 Diisostearate/ Polyhydroxystearate/Sebacate | 3.0 |
Phase B | ||
Deionized Water | Aqua | 49.0 |
Optiphen | Phenoxyethanol, Caprylyl Glycol | 1.0 |
Glycerin | Glycerin | 3.0 |
Magnesium Sulfate | Magnesium Sulfate | 1.0 |
Procedure
- Combine Phase A ingredients and heat to 85 °C.
- Combine Phase B ingredients and heat to 85 °C.
- Once both Phases are at temperature, add Phase B to Phase A and increase mixing speed. Shear is optional.
- When emulsion is smooth, pour at 67-72 °C into appropriate containers. Keep mixer on during filling.
formula #3:
Propel/Repel Water in Silicone Foundation Stick.
Hard stick for propel tubes will generally require penetration around 20-40 dmm.
1. Design water phase
2. Design oil phase:
2.1. Dimethicone is the main oil phase ingredient.
2.2. Wax selection and % usage: Ozokerite Wax
2.3. No Gel Chart Available therefore:
2.3.1. Lab gel tests done using 5, 10 and 15% wax to determine structure needed.
2.3.2. The melt point of Ozokerite Wax is 70 -78 °C, hence processing temperature will be 85 °C or more
2.4. The emulsifier was chosen due to compatibility
2.5. Measure congeal point of the oil phase. Results: 74 °C
2.6. Therefore, pour temperature will be 79-84 °C
3. Final formula hardness = 34.5 dmm
Multi Use Colour Stick
Formula 9/23-451-358-883-3
Ingredient Trade Name | INCI Name | % |
---|---|---|
Phase A | ||
Ozokerite 175 | Ozokerite Wax | 4.2 |
Synkos 2060 | Synthetic Wax | 7.0 |
Kester Wax K-24 | Lauryl Laurate | 4.2 |
Dow ES 5300 | Lauryl PEG-10 Tris(Trimethylsiloxy) silylethyl Dimethicone | 3.0 |
BELSIL DM 1 Plus | Dimethicone | 19.5 |
Olive Squalane | Squalane | 7.1 |
Zinc Stearate USP | Zinc Stearate | 0.5 |
UnipureWhite LC-987 AS-EM | CI 77891 (and) Triethoxycaprylylsilane | 3.19 |
Unipure Red LC-381 AS-EM | CI 77491 (and) Triethoxycaprylylsilane | 0.06 |
Unipure Yellow LC-182 ASEM | CI 77492 (and) Triethoxycaprylylsilane | 0.45 |
Unipure Triple Black LC990 AS-EM | CI 77499 (and) Triethoxycaprylylsilane | 0.04 |
Phase B | ||
Deionized Water | Aqua | 45.76 |
Optiphen | Phenoxyethanol, Caprylyl Glycol | 3.0 |
Glycerin | Glycerin | 1.0 |
Magnesium Sulfate | Magnesium Sulfate | 1.0 |
Procedure
- Combine Phase A ingredients and heat to 85-90 °C.
- Combine Phase B ingredients and heat to 85-90 °C.
- Once both Phases are at temperature, add Phase B to Phase A and increase mixing speed.
- Continue to mix while cooling to 84C.
- Pour into containers.
formula #4:
Tinted emulsion.
Creamy W/O emulsion for both jar or pump. No penetration value.
1. Design water phase
2. Design oil phase:
2.1. CCT was chosen as the main oil
2.2. Wax selection and % usage: Kester Wax BWR
2.3. According to Chart #4, 2% Beeswax with CCT as the main oil should yield the desired penetration. BWR is a vegan alternative.
2.3.1. The melt point of BWR is 62 -66 °C, hence processing temperature will be 75 °C or more
2.4. The emulsifier was chosen due to compatibility.
2.5. Formula should be thickened and still pumpable. Therefore, process is to mix and pour at 45°C
Hydrating Tinted Face Cream (SPF)
Formula 8/23-358/837-3
Ingredient Trade Name | INCI Name | % |
---|---|---|
Phase A | ||
JeechemCTG | Caprylic/ Capric Triglyceride | 17.0 |
JeechemSqualane | Squalane | 5.0 |
AkolinePGPR | Polyglyceryl-3 Polyricinoleate | 2.0 |
Kester Wax K-24 | Lauryl Laurate | 5.0 |
Kester Wax K-BWR | Behenyl Behenate, Polyhydroxystearic Acid, Euphorbia Cerifera (Candelilla) Wax | 2.0 |
UnipureBrown LC 8814 | CI 77499 (and) CI 77491 (and) CI 77492 | 0.6 |
UV Cut ZnO-68-CG5 | Zinc Oxide, Caprylic/Capric Triglyceride, PolyhydroxystearicAcid | 22.1 |
Phase B | ||
Deionized Water | Aqua | 40.85 |
Optiphen | Phenoxyethanol, Caprylyl Glycol | 0.5 |
Glycerin | Glycerin | 3.0 |
Sodium Chloride | Sodium Chloride | 0.5 |
Magnesium Sulfate | Magnesium Sulfate | 0.5 |
Procedure
- Combine Phase A ingredients and mix well, while heating to 85 °C. Homogenize, if necessary, to ensure ZnOis well dispersed.
- Combine Phase B ingredients and heat to 85 °C.
- Once both Phases are at temperature, add Phase B to Phase A and increase mixing speed.
- Cool to 55 –60 °C and homogenize at 5000 rpm.
- Continue to cool with propeller mixing to fill temperature